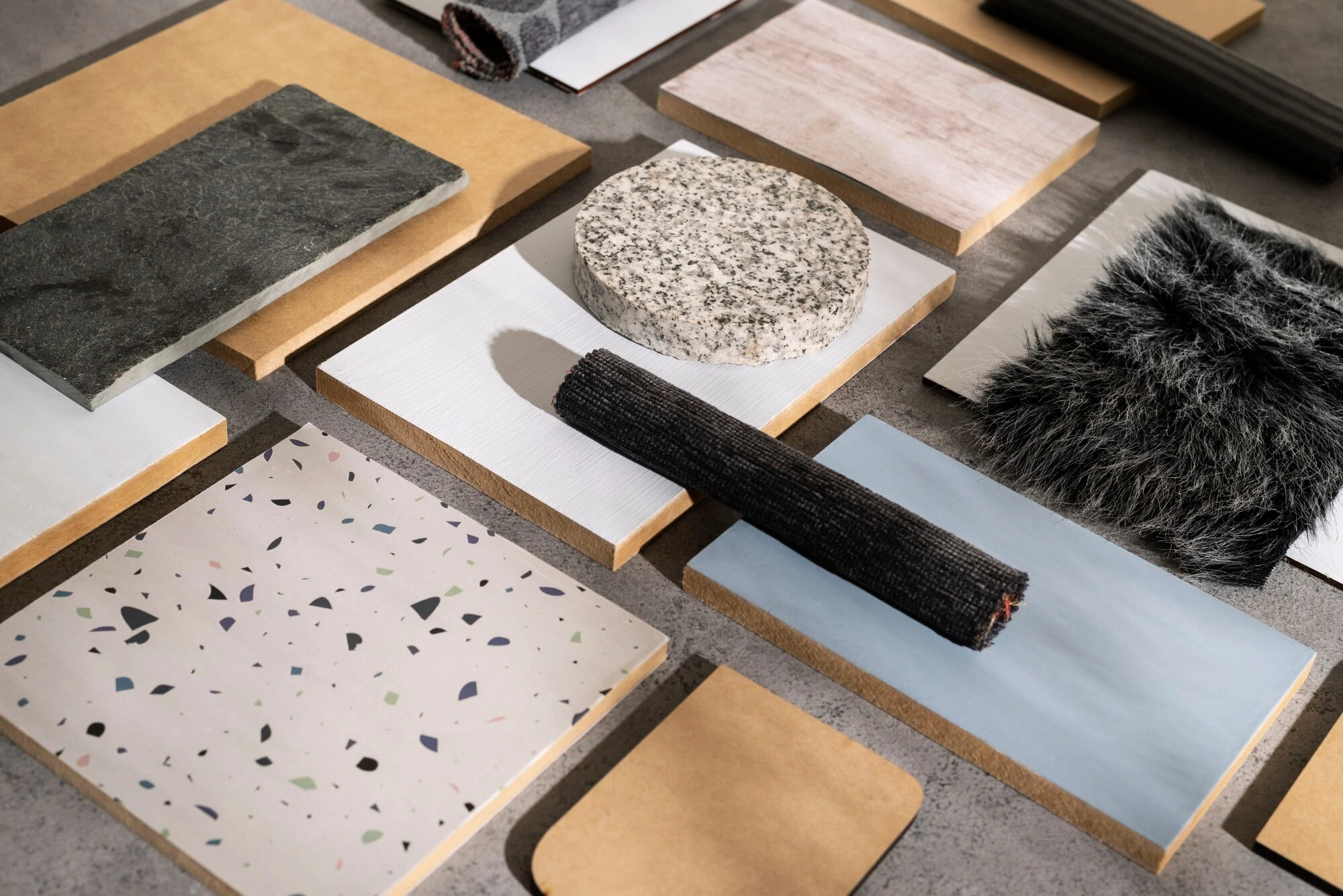
The A To Z Of Ceramic Tile Production: How Tiles Are Made
Spenza Ceramics has become an industry standard for premium quality tiles. To conquer this peak, we worked day and night to improve and innovate our tile manufacturing process and bring the best quality tiles to you. Have you ever wondered what goes into making these premium tiles?
Today, we will take you through the entire process of how the best quality ceramic tiles are made, from sand to brand. Let us take you into the factory, unravel how we make ceramic tiles, and ship them to the dealers.
How Tiles Are Made: The Production Lifecycle
Ceramic tile production passes through various stages that add to the aesthetics, durability and additive properties of the tiles.
1. Raw Materials
– Tiles are made from essential ingredients that are readily available in nature. A ceramic tile “bisque” is made using different components like:
a) Clay
b) Feldspar
c) Pottery Stone
d) Silica Sand
e) Talc
– The raw materials are sourced from quarries and stored in the factory/plant, where they are graded before mixing.
After mixing the raw material in specific proportions, the raw material composition is then transferred to large mixing tanks along with water and ceramic pellets to form a liquid called “slurr
2. Slurry
– With the help of drainage pipes, the slurry is then transferred to large underground storage tanks.
– Multiple heavy-duty motors keep rotating and mixing the slurry so that it doesn’t form lumps.
3. Spraying Slurry Into Atomiser Or Spray Dryer
The slurry is transferred to a machine called the atomiser or spray dryer. In simple words, here’s what happens in the atomiser:
– The liquid slurry is sprayed inside the atomiser tank with a nozzle.
– Hot air is pushed into the tank that vaporises the water & moisture in the slurry.
– Once the water evaporates, powder remains, which is transferred to a conveyor belt below the atomiser tank.
This process turns slurry into a powder form called atomised powder.
4. Pressing The Powder Under A Hydraulic Press
– Then comes the process of using a heavy-duty hydraulic press that presses the atomised powder into a mould.
– The hydraulic press puts a pressure of 1000 tons, turning the powder into a solid bisque or slab.
5. Drying The Raw Tile Base
– The slab of sand mixture is then dried to further eliminate any residual moisture.
– It is very crucial that the tile base or slab is completely dry before putting it into the kiln.
– If there is moisture in the slab, then it may blast into the kiln during the firing process and damage the machine along with other articles of the batch.
– The tiles are put through a pre-kiln stage, where they are heated in an oven at 300-500 ℃, which ensures the tiles are free from physical weakness like warps or defects like cracks
6. Glaze Application
– A shiny layer on the surface of the tiles, called Glaze, is applied. This layer will become like glass on heating.
– The glaze is also made of various compounds like:
a) Glass Formers: Silica and Feldspar
b) Fluxes: Soda Feldspar, Calcium Carbonate, Boric Oxide, & Dolomite.
c) Stabilisers: Alumina and Kaolin
d) Additional Ingredients: Cullet, Limestone, Fly Ash and Pozzolanic Waste, Colorants and Opacifiers.
– After mixing the different proportions of these compounds in large mixing bowls, the liquid glaze is pumped to the production line, where a thin layer of it is applied to the tiles.
– It can be applied through spray, waterfall or screening methods.
– Then, the tiles are left at room temperature for the glaze to cool down.
7. Printing Designs On the Tile
– Now, all the mesmerising designs are printed on the tiles.
– This can be done using roller screens or digital printers.
– Modern tile manufacturers use high-tech printers that can print any design in just seconds.
8. Kiln – Fire The Tiles
– After printing and glaze application on the tile, they are fired into the kiln.
– The batch of tiles is passed through a very long conveyor belt-type kiln that fires the tiles from 700 to 1500 ℃.
– This process not only hardens the tiles but also makes them durable enough to withstand heavy loads without breaking.
9. Sizing & Polishing
– Once the tiles come out of the kiln, they are left to cool down naturally.
– They are further processed to the sizing machine, where they are cut into the perfect size and polished with abrasives to smoothen the tile’s surface.
– Then, nanomachines apply the nano chemical evenly across the tile surface, preventing stains and moisture from affecting the tiles.
10. Packaging & Shipment
– After sizing and polishing, the tiles are ready for shipping.
– They are stored in the factory warehouse and dispatched to dealers across India.
Key Takeaways
This was the entire journey of how ceramic tiles are made that adorn the walls and floors of residential and commercial spaces. This entire process covered how various coatings on the tiles protect them from stains and damage while heating them to extreme temperatures adds to their durability and shelf life.
Dock up your tile showroom with the best tiles from Spenza Ceramics and let their beauty attract profits for your business. Contact us today or visit our website to choose the best-in-class ceramic tiles that are perfect for every space.
Frequently Asked Questions
1.What materials are used to manufacture ceramic tiles?
Ans. Ceramic tiles typically combine refined clays, such as kaolin, along with sand, feldspar, and water, to from the perfect slab of beauty.
2. Why should you choose tiles for flooring and walls?
Ans. Tiles offer durable, moisture-resistant surfaces with countless designs, making them easy to clean, long-lasting, and visually appealing for both floors and walls.
3. How are designs printed onto ceramic tiles?
Ans. Modern methods use advanced digital inkjet printing, applying high-definition patterns directly onto tile surfaces before glazing and firing for lasting vibrancy.
4. Is ceramic tile better than marble?
Ans. While marble exudes natural elegance, ceramic tiles offer affordability, easier maintenance, scratch resistance, and vast design options, making them equally appealing.
5. Where can ceramic tiles be effectively installed?
Ans. From bathrooms and kitchens to living rooms, parking and commercial spaces, ceramic tiles can elevate the aesthetic and charm of every space.

Explore our full range of Tiles
Find the perfect tiles for your area with our huge range of styles, colours, and finishes, No matter you are looking tiles for kitchen, bathroom, parking, exterior or interior spaces, we have it all.
Shop Now